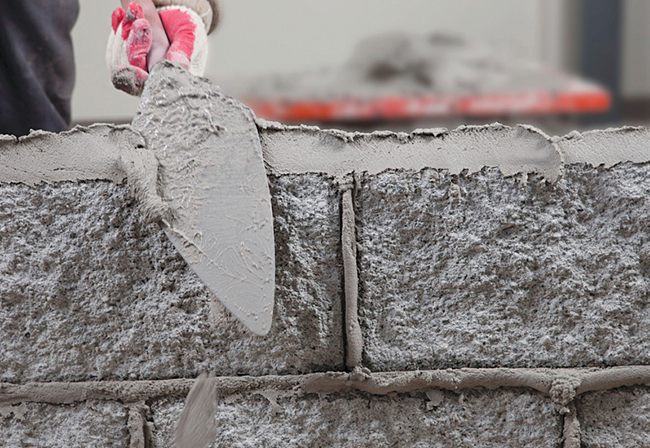
HPMC Cellulose For Wall Putty
HPMC stands for Hydroxypropyl Methyl Cellulose. It is a non-ionic cellulose ether derived from natural polymer cellulose. HPMC is made by treating cellulose with methyl chloride and propylene oxide, resulting in a chemical structure with both hydroxypropyl and methyl groups attached to the cellulose backbone.
HPMC is widely used in various industries such as construction, pharmaceuticals, food, cosmetics, and personal care products due to its versatile properties. Some of its key characteristics include:
-
Thickening: HPMC can significantly increase the viscosity of liquid formulations, making it a common thickening agent in many products.
-
Water Retention: It has excellent water retention properties, which is particularly useful in construction materials like cement mortar and wall putty, as well as in personal care products like lotions and creams.
-
Film Formation: HPMC can form a protective film when applied to surfaces, making it useful in coatings, paints, and adhesives.
-
Binding: It acts as a binder in tablet formulations in pharmaceuticals, helping to hold the active ingredients together.
-
Stabilization: HPMC helps stabilize emulsions and suspensions in food, cosmetics, and pharmaceuticals, preventing separation of ingredients.
-
Surface Tension Reduction: It can lower the surface tension of liquid formulations, improving wetting and spreading properties.
-
Controlled Release: In pharmaceuticals, HPMC is used in controlled-release dosage forms to regulate the release of active ingredients over time.
HPMC is available in various grades with different viscosity ranges, particle sizes, and other properties to suit different applications. Its versatility and compatibility with other ingredients make it a popular choice in a wide range of products and industries.
HPMC (Hydroxypropyl Methyl Cellulose) is commonly used in wall putty formulations for various reasons. Here's how it is beneficial in wall putty:
-
Water Retention: HPMC helps in retaining water in the wall putty mix, ensuring prolonged workability and preventing premature drying. This is crucial for achieving a smooth and uniform finish on the wall surface.
-
Improved Workability: By controlling the water content and enhancing the rheological properties of the putty mix, HPMC improves workability. This makes it easier to apply the putty evenly onto the wall surface, reducing the effort required for smoothing and finishing.
-
Reduced Shrinkage: HPMC can help reduce shrinkage during the drying process of wall putty. This minimizes the occurrence of cracks or surface imperfections after application, resulting in a more durable and aesthetically pleasing finish.
-
Enhanced Adhesion: HPMC enhances the adhesion of wall putty to various substrates, including concrete, plaster, and masonry. This ensures that the putty adheres firmly to the surface, preventing it from peeling or flaking over time.
-
Sag Resistance: In vertical applications such as filling holes or repairing cracks, HPMC helps prevent sagging or slumping of the putty, allowing it to maintain its shape and thickness until it sets.
-
Improved Spreadability: HPMC cellulose ether contributes to the smooth and creamy texture of wall putty, making it easier to spread evenly across the surface without lumping or clumping.
-
Enhanced Durability: The use of HPMC in wall putty formulations can improve the overall durability and longevity of the coating by providing better resistance to weathering, moisture, and other environmental factors.
When using HPMC in wall putty, it's essential to follow recommended guidelines regarding dosage and mixing procedures. Typically, it is added to the dry mix and dispersed uniformly before adding water. The exact dosage may vary depending on factors such as the desired properties of the putty and the substrate conditions.
HPMC is a versatile additive that plays a vital role in enhancing the performance and application properties of wall putty, leading to smoother, more durable, and aesthetically pleasing wall finishes.