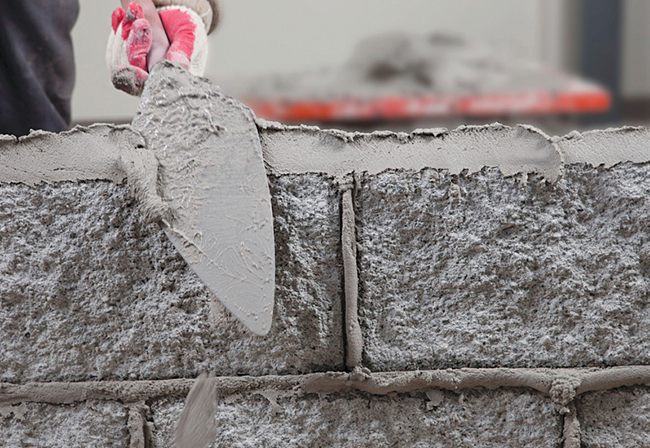
The Detail Description Of Cellulose Ether HPMC
Introduction to Cellulose Ether HPMC: Cellulose Ether Hydroxypropyl Methylcellulose (HPMC) is a semi-synthetic polymer derived from cellulose, the main component of plant cell walls. HPMC is created through a chemical process involving the modification of cellulose with propylene oxide and methyl chloride. This versatile polymer finds extensive use in various industries due to its unique combination of properties, with a particular emphasis on its applications in the construction sector.
Key Properties of Cellulose Ether HPMC:
-
Water Solubility: HPMC is soluble in water, with its solubility increasing as the temperature rises. This property allows for easy incorporation into water-based formulations.
-
Film-Forming Ability: HPMC exhibits excellent film-forming properties, making it ideal for coating applications in various industries.
-
Viscosity Control: With the ability to modify viscosity, HPMC serves as an effective thickening agent, influencing the rheological properties of solutions and formulations.
-
Surface Tension Reduction: HPMC reduces surface tension, improving wetting properties and aiding in adhesion in applications like paints and coatings.
-
Thermal Gelation: HPMC cellulose ether can form gels at elevated temperatures, providing versatility in applications where thermal responsiveness is required.
Applications of HPMC Cellulose Ether in Construction Materials:
-
Mortars and Cement-Based Products:
- Acts as a water-retaining agent, enhancing workability and preventing premature drying.
- Improves adhesion, durability, and consistency of mortars and cement-based formulations.
-
Tile Adhesives and Grouts:
- Enhances the workability and adhesion of tile adhesives, ensuring proper bonding to substrates.
- Improves consistency and water retention in grout formulations.
-
Plasters and Renders:
- Controls consistency and adhesion in plaster formulations.
- Enhances workability, allowing for smoother application and finishing.
-
Self-Leveling Compounds:
- Improves flow and leveling properties in self-leveling compounds, ensuring a smooth and even surface.
-
Exterior Insulation and Finish Systems (EIFS):
- Enhances the adhesion of finish coats to insulation boards.
- Contributes to the workability and durability of EIFS coatings.
-
Gypsum-Based Products:
- Improves workability, adhesion, and water retention in joint compounds and gypsum plasters.
-
Concrete Additive:
- Acts as a viscosity modifier and water reducer in concrete formulations.
- Enhances pumpability and reduces water demand without compromising performance.
-
Extruded Building Products:
- Improves processing characteristics in extruded building products like insulation boards.
-
Hydraulic Lime Mortars:
- Enhances workability and adhesion in the restoration of historic buildings using hydraulic lime mortars.
Conclusion: Cellulose Ether HPMC stands as a versatile and indispensable component in construction materials, contributing to improved performance, workability, and durability across a wide range of applications in the construction industry. Its unique combination of properties makes it a valuable additive, playing a crucial role in shaping the characteristics of various formulations.